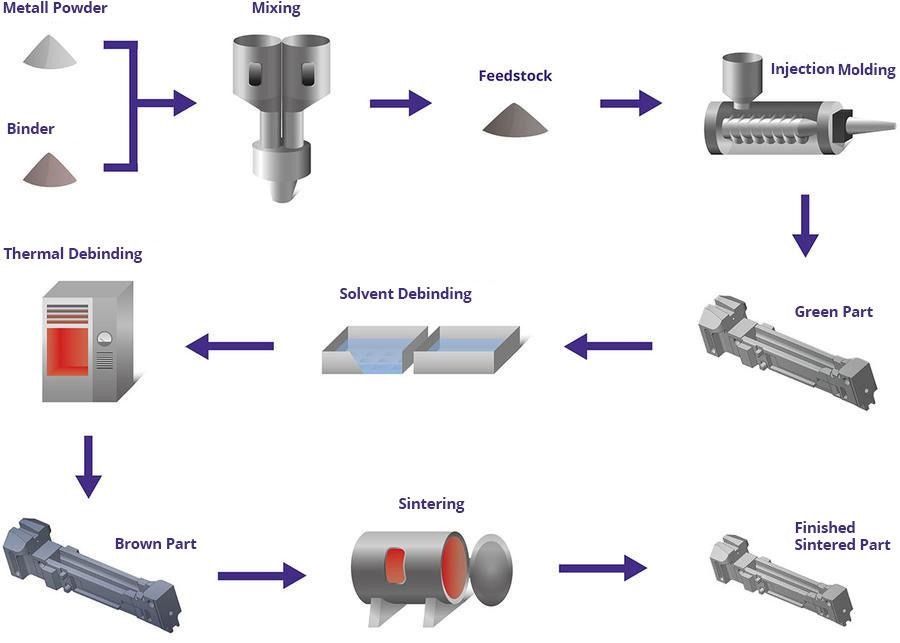
Overview
Metal Injection Molding (MIM) process is a combination of plastic injection molding and powder metallurgy technologies. To obtain the necessary chemical and physical properties, powders are selected by size and shape and complemented with additives. Every particle of the powder is coated with binder components, which transport the powder for molding and gives the final form rigidity. The metal injection molding is very suitable for high volume production of complex design with tight tolerances.
Pre-sales Assessment
FineMIM pre-sales team will work closely with you to assess the feasibility for MIM production in terms of cost, material, or manufacturing. FineMIM will also advise how to change design for achieving the best effect through Metal Injection Molding.
1. Feedstock Mixing and Granulating
Very fine metal powders usually (<15 microns) are mixed with a primary paraffin material and a secondary thermoplastic polymer. Together they act as binders.
Unlike standard powder metalurgy, which can achieve only 80-90% of theoretical density, MIM results in 95-100%. This means we can achieve close tolerances and reduce costs by producing small, complex parts over high production runs.
2. Injection Molding
The feedstock is fed into either our multi-slide Metal Injection Molding machinery or standard molding equipment, then heated and injected into a mold cavity under high pressure.
Our proprietary multi-slide tooling can produce extremely complex shapes and allow for shorter cycle times.
Once molded, the component is referred to as a “green part”.
Our multi-slide process routinely produces green parts in 3 seconds as opposed to 25-40 seconds on a standard MIM system.
Its geometry is identical to that of the finished piece, but to allow for shrinkage during the sintering phase, it’s about 20% larger in size than the finished component will be.
3. Debinding
Binder removal or “debinding” involves a controlled process to remove most of the binders.
The process removes the binders and prepares the part for the final step – sintering.
Once debinding is complete, the component is referred to as “brown part”.
4. Sintering
The “brown part” is held together by a small amount of the binder, and is very fragile.
Sintering eliminates the remaining binder and gives the part its final geometry.
During sintering, the part is subjected to temperatures near the melting point of the material.
The entire sintering process takes 15-20 hours.
Secondary Operations
To improve material properties, achieve tight tolerances, enhance cosmetic surface, or assemble other components, MIM parts can be heat treated, CNC machined, PVD coated, or welded.