MIM has become a synonym for the iPhone SIM card tray and camera lens protector ring in the 3C industry. In addition to these, however, precision parts in e-cigarettes are also manufactured using Metal Injection Molding. The metalworking process on the market is probably not as fast as the MIM process. As long as the specifications and the measured dimensions of the samples are confirmed, efficient and fast processing can be realized. This advantage has been reflected in the mobile phone card tray and camera accessories.
In 2018, sales of mid-range and high-end smartphones declined, and MIM products used in smartphones are gradually decreasing. However, in the electronic cigarette industry, the MIM advantages have emerged, most of the metal parts in electronic cigarettes can be produced by MIM process. As an emerging product, e-cigarettes are close to the taste of cigarettes, which is more beneficial to smokers than cigarettes. Although the policy on e-cigarettes is not yet fully mature, the number of e-cigarette users has increased significantly, and there are currently at least 20.8 million e-cigarette users worldwide. Consumer demand naturally leads to an increase in the number of products, and the MIM process that can achieve high-efficiency processing is indispensable for the processing of electronic cigarette parts.
Compared with casting, machining, pressing and other processes, MIM (metal injection molding) process is more efficient and precise. The metal injection molded products are small and precision stainless steel parts, dimensional tolerance, thin wall and hole depth can achieve high precision. The complex shape, small size and high output of the parts are the advantages of the MIM process. At present, related accessories in electronic cigarettes have been involved in MIM manufacturing, such as cigarette holders, atomizer bases, and outer cases.
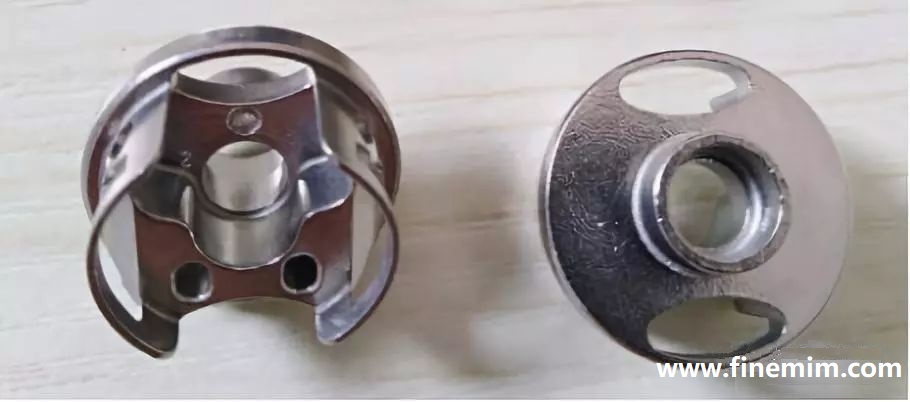