The MIM strengths of complex shapes, smaller sizes, and large production volumes have found numerous applications in smartphone, watches, hand tools, locks, surgical tools, orthodontic brackets, automotive engine parts, firearms, electronic packages, cutting tools, and sporting devices.
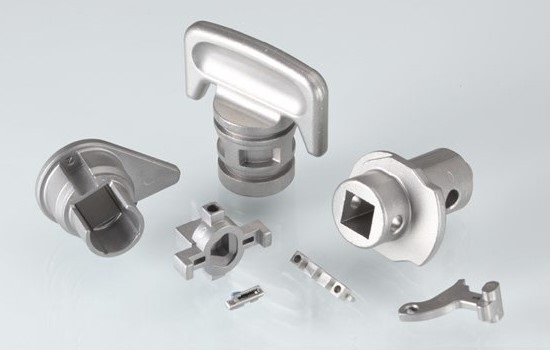
To summarise this quick guide, the criteria for identifying a MIM candidate are captured in a few key considerations:
- Mass/volume
MIM is excellent at reducing fabrication costs for components where much material loss would occur in machining or grinding - Quantity
Tooling and set-up costs are difficult to justify for low production quantities, so MIM works best when annual production quantities exceed 20,000 per year - Material
MIM is most attractive for designs that use hard to machine materials such as titanium, stainless steel, and nickel alloys - Complexity
MIM is best applied to complex geometries, it works best on components that require multiple axes for indexing in machining - Performance
If performance is important, then the high density in MIM generates properties that usually are competitive - Surface finish
The surface roughness reflects the initial particle size, yet controlled textures are possible at almost no cost penalty, unlike competitive processes - Tolerances
MIM tends to have a high cost from secondary operations if tight tolerances are required, the as-sintered tolerances are probably on ± 0.3% - Assembly
Benefits arise when multiple parts can be consolidated into a single piece to save on inventory and assembly costs - Blemishes
MIM has inherent blemishes that must be located in noncritical positions or removed after fabrication; examples include gates marks, ejector pin marks, or parting lines - Novel compositions
MIM can form novel material combinations that are difficult via traditional processes, for example laminated or two-material structures or mixed metal-ceramic materials for wear applications.
Metal injection molding leads to outstanding success when the design anticipates MIM fabrication and invites expert participation.
Review by an advisor knowledgeable with MIM invariably leads to lower costs, better quality, longer mould life, and good reconciliation between intended function and the MIM process attributes.
Many materials are available via MIM process, but a few are dominant. When the material is difficult to machine, such as tool steels, titanium, nickel alloys, or stainless steel, then the net-shape aspect of MIM is most beneficial.
Component geometric features need not be sacrificed for MIM, but there are certain geometric characteristics where the technology is most successful.
The properties attainable via MIM process vary between production sites; however, the many properties converge to the range customarily found in engineering handbooks. Now we are seeing new MIM materials, custom designed for the process. These include laminated (hard-soft, magnetic-nonmagnetic, and conductive-insulator) structures, foamed metals, and hollow objects. These options propel MIM into areas where there are few alternative technologies.