Component fabrication for medical devices must often enable the manufacture of strong, durable parts in intricate shapes and designs. The ability to mold metal in an injection molding process moves developers much closer to this goal. The fact that the process can be offered relatively quickly makes metal injection molding a very desirable fabrication method for medical device design engineers.
Metal injection molding (MIM) is a manufacturing process used for more than 25 years to produce intricate metal parts that have mechanical properties similar to wrought materials. MIM is a cost-effective option for prototyping and producing low- to mid-volumes of medical device components–in weeks, rather than months.
Combining the flexibility of injection molding with the durability and strength of metal, MIM can be used to produce parts that are difficult or impossible to efficiently manufacture through other means of fabrication. Part complexity that would be cost prohibitive due to multiple machining operations or by casting and then finishing, can be achieved cost effectively through MIM processing.
The more geometrically complex the part is, the stronger the rationale for manufacturing it using MIM. Parts can include irregular shapes, splines, undercuts, side holes or grooves, or complex contours. Parts that would typically be made by assembling multiple components often can be designed as a single MIM part.
It’s even possible to use MIM for low volume and prototype quantities. Turnaround times of 15 business days or less, volumes between 25 and 5,000+ pieces, and low cost of entry (mold and sample parts for less than $5,000) are all available with MIM services.
MIM vs. Other Metal-Forming Processes
Compared to machining, MIM offers a cost advantage for parts with more complex features, an advantage that amplifies as quantities increase. Because MIM is a molding process where minimal excess material needs to be removed, it saves time and material as compared to machining the part. This results in time and money savings for medical device manufacturers.
Investment casting is a labor intensive process that is better suited for producing small quantities of parts, and typically has a higher cost-per-part than metal injection molding. MIM also provides better surface finishes than investment casting, creating smoother parts with thinner walls. MIM offers the ability to scale up production cost effectively, helping medical suppliers meet high volume production schedules.
MIM offers superior density and strength for critical medical components, compared to conventional powdered metal components. MIM also provides the ability to produce more geometrically complex parts for demanding medical applications.
Medical Applications
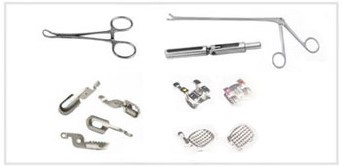
MIM is among the most cost-effective ways to manufacture highly complex medical parts in a wide variety of materials. Over the past 15 years, due to its ability to produce high volume components to net-shape, MIM has become an essential manufacturing technology for the medical device industry.
Using MIM, product designers select material properties for their medical application, including hardness, corrosion resistance, and strength. A variety of metal powders are used for MIM, and stainless steels are the most prevalent. The 316L composition I is often used due to its combined strength and corrosion resistance. Adjusting the alloy element ratios can also create materials with specific properties.
MIM enables the production of microsize parts and intricate medical components with features such as threads or undercuts that are not possible using traditional manufacturing processes. Among the first major MIM applications was orthodontic brackets, which continue to be a major product for the industry. Typically, these extremely small precision parts are made from 316L stainless steel.
Another medical application for MIM is articulation gears for surgical staplers that are produced to net shape from 17-4 PH stainless steel. Other applications include a base plate for implantable infusion pumps, surgical instruments, and knee and other orthopedic implant parts.
MIM Process
MIM uses fine metal powders (typically less than 20 micrometers) that are custom formulated with a binder (various thermoplastics and other materials) into feedstock pellets. These pellets are then fed into a hopper on an MIM press, which is nearly identical to a standard plastic injection molding press.
Inside the press, pellets are heated using electric heaters and screw motion, and the feedstock is injected into a tool. After solidification, the parts (referred to as green parts before debinding and sintering) are ejected from the press, de-gated, and placed on ceramic substrates, or setters. The setters help the parts retain their shape during the debinding and sintering process.
Next, the green parts are loaded into a debind oven where most of the binder is extracted through thermal, solvent, or catalytic processing. The resulting (brown) parts are fragile and approximately the same size as the green parts but only 80 percent as dense. Just enough binder remains to keep the powder particles together.
Finally, the parts are sintered, or solid-state diffused, in a controlled-atmosphere sintering furnace at temperatures close to the metal’s melting point. After the parts are sintered, they have properties similar to wrought materials.
During the sintering cycle, the remaining binder is removed–as well as the air space that was created when the binder was removed –and the parts shrink approximately 20 percent to their final size. MIM molds need to be oversized to account for this shrinkage during the sintering process.
Design Considerations
The mass of MIM parts is typically less than 150 grams, and the average part is closer to 10 grams. As part size increases, MIM’s cost advantages become off-set by the high raw material costs.
Ideally, MIM parts should have wall thicknesses not less than 0.1cm (0.04in.) and not more than 12.7mm (0.5in.). Due to material flow limitations, care should be taken to minimize the distance from the gate to the part’s farthest point. MIM part tolerances are nominally [+ or -] 0.5 percent, although in some cases, tighter tolerances can be achieved.
Since MIM parts shrink and become soft during sintering, parts should be designed for proper support throughout the sintering process to ensure that they maintain their desired shape. The easiest parts to sinter have a common co-planar surface that can rest flat on a ceramic substrate or setter. When unsupported features are present, support often needs to be added through special fixturing to minimize or eliminate distortion of the part.
Compatible with Other Processes
Many parts are sintered to final dimensions because the tolerance for the MIM process falls within [+ or -] 0.5 percent. If tighter tolerances are required, secondary metalworking operations can be performed. MIM parts can be machined, tapped, drilled, broached, sized, ground, or welded like wrought parts.
Conclusion
MIM offers the same design freedom as plastic injection molding and is an excellent option for relatively small, highly complex parts that otherwise would require extensive finish machining or assembly operations if made by any other metal-forming process.
For more information, please visit www.finemim.com.