Micro MIM (μ-MIM) is an advanced method of metal injection molding, using sub-μm-sized metal powders and very fine molds to produce extremely small three-dimensional structures with very high resolution, sharp edges, and outstanding aspect ratios while the cheap and well-established method of injection molding is applied.
Powder injection molding (PIM), which encompasses metal powder injection molding (MIM) and ceramic powder injection molding (CIM) is a net-shape process for the manufacturing of high volume and high precision components for use in a variety of industries. In these conventional MIM products, as the size become smaller, the dimensional accuracy becomes higher as it falls within a few tenth micrometers. As the size of MIM products decreases much further, the dimensional accuracy is hoping to ensure within a few micrometers. In practical productions, however, it cannot be achieved easily. The production method of these tiny metallic parts which have micro-size and micro-structure are called μ-MIM, which is capable of manufacturing the micro-structured parts such as micro-pillars.
The micro-miniaturization of dimension and structures in MIM is facing with various technical problems, such as incomplete filling to narrow cavity, failure in demolding of fragile green compacts, and deformation in debinding and sintering process. Therefore micro MIM (μ-MIM) process is a more sophisticated process for tiny metal components and micro structured parts.
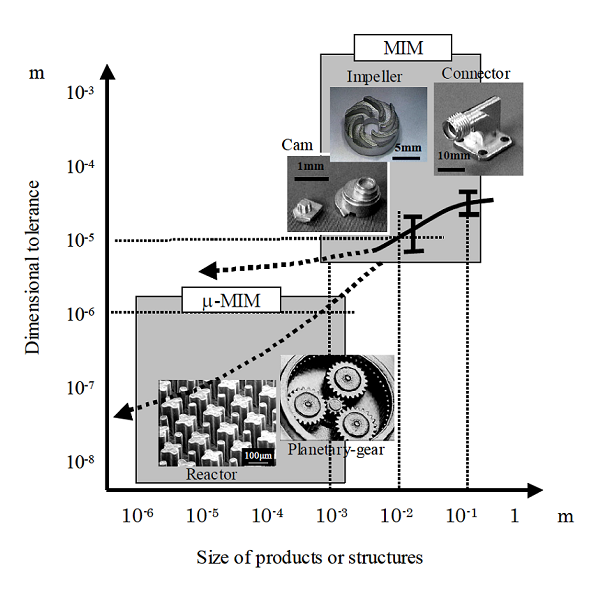
The μ-MIM process is very useful for the manufacturing of micro-sized and microstructured metallic parts, but it is facing with various technical problems in each process. For example, it is difficult to fill feedstock completely into a narrow cavity and to demold fragile green compacts from a metallic mold in injection molding process. A careful handling is also required in the debinding and sintering processes. There are many other technical problems such as measuring of the density, the shape and mechanical properties of sintered parts.