Complex, high-volume parts are ideal for this process.
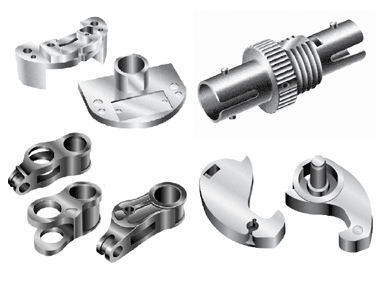
For high-volume, high-precision needs of many automotive applications, metal injection molding (MIM) is a growing, though largely overlooked, process that could result in significant cost savings.
Industry statistics state the overall process has grown from $9-million in 1986 (the original patents were awarded in 1980) to $382-million in 2004 to more than $1.5-billion in 2015. The sweet spot for metal injection molding covers high-volume, small parts of relative complexity. For automotive, this includes brake components, rocker arms, injector nozzles, and numerous fittings and connectors.
The concept of using the injection molding process familiar to plastics processors to shape a metal excites many design engineers, especially when they learn the final part properties are the same, if not better, compared with most machining processes. MIM succeeds in part because there is little material loss; typically 98 percent of the purchased raw material ends up in final products.
Most common engineering alloys can be injection molded, but about 30 alloys dominate the applications. The most popular alloys are austenitic stainless steels (AISI 304L and AISI 316L). After injection molding a combination of the metal powder and a polymer binder, the binder is extracted and metal particles are subjected to a high-temperature sintering treatment. Capillary forces between the small particles make the resulting structure very dense and give it a slightly shrunken component that is essentially full density with tensile and hardness properties equivalent to handbook values.
Metal Injection Molding Process
One of the keys to economic success is to apply MIM to complicated geometries, those that already require extensive machining. Further gains come by adding cores, holes, or other mass-reduction features, which can advance lightweighting goals. MIM excels when the component complexity is high and performance demands require excellent properties. It wins against casting since it has better dimensional control and a smoother surface finish. MIM is best applied to large production quantities, as it does require mold tooling. Several parts have reached production quantities in excess of 10-million parts per year.
Most of the metal or ceramic powders used in MIM are between 1 and 40 µm. Typical ratios are about 60 percent metal powder and about 40 percent polymeric binders. Depending on the metal powder, a steel or stainless steel mixture constitutes about 94 percent powder by weight. Lower-density powders may range to 86 percent powder and high-density powders like tungsten may require as much as 97 percent powder. Binders melt at relatively low temperatures to allow easy mixing and molding. The combination of powder and binder is termed “feedstock” and is available from a number of suppliers. Many firms mix feedstock to their own specifications.
MIM vs Traditional Powder Metallurgy
Some engineers confuse MIM with traditional press-sinter powder metallurgy (PM). Standard powder metallurgy forming relies on vertical axis compaction to press a coarse powder into a compact shape. Die compaction is best at forming squat shapes that are easily ejected from the tooling. The ejection step requires the sides be parallel, a restriction in geometry not required for MIM. Thus, in MIM undercuts and holes are possible perpendicular to the main axis.
Dimensional control is the critical difference. MIM components are formed with uniform density and the scatter in final component mass and dimensions is small. For PM, the standard protocol is to use larger powders versus MIM and to sinter at lower temperatures for shorter times to avoid distortion during sintering densification, resulting in lower properties. As a result, MIM strengths are about two-fold higher than PM. Fatigue strength is more than three-fold that of PM, and impact toughness is eight-fold higher.
Automotive applications for MIM started to escalate with use in turbochargers, fuel injectors, control components (clock mounts, entry locks, knobs and levers), and valve lifters. The process has found global acceptance.